
By Corporate Intelligence Advisors
Theory of Constraints in Manufacturing
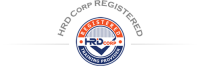
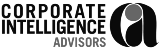

By Corporate Intelligence Advisors
![]() |
![]() |
![]() |
![]()
|
Theory of Constraints in Manufacturing
Training Category:
Manufacturing Operations
Duration:
2 Days
Target Audience:
Anyone from production and manufacturing industries who are interested in evaluating the Theory of Constraints as an improvement methodology will be benefit from attending this workshop. In particular, executives and managers who are seeking a way to improve their organization by introducing a new culture of change will find that this programme provides an excellent, in-depth introduction to the TOC Methodology. Typically, they're heads, managers and executives from the following departments:
- Production
- Manufacturing
- Plant
- Operation
- QA
Dec 2015 ›
Hotel Capitol, Kuala Lumpur, Malaysia
Schedule:
Mon 14 Dec 2015 - Tue 15 Dec 2015
8:30AM - 5:30PM
Fee Per Person:
RM2,044.00
Promotions:
- Register not later than 12 Oct 2015 for only RM1,844 per person.
- 10% discount for group registration of 5 paxs or more from the same organization.
- Mystery Door Gift for all our participants.
- 10% discounts will be given to our participants who wish to attend our Professional Administrative Conference in 2016.
* Other terms & conditions apply.
![]() |
Request for Quotation |
![]() |
|
![]() |
- Language: English
- PowerPoint Presentation
- Workshop
- Group Discussion
- Presentation Handouts
- Reading Materials
- Indoor Activities
- Simulation
- Participant Presentation
- Role Play
- Lecture
- Case Studies
- Demonstrations
- Certificate of Participation
Course Introduction ›
What is Theory of Constraints (TOC) and its Benefits to the Production Industries?
Theory of Constraints (TOC) is a holistic, step-by-step management methodology developed for organizations in search of rapid improvement. TOC gives managers a way to find their biggest leverage point for improvement, so that available resources can be allocated where they will have the most impact on helping to reach the goals. TOC uses precise cause-effect logic to drill down through layers of symptoms to identify underlying problems. The TOC methodology has been successfully applied to all areas of for profit and not-profit organizations including production, logistic, project management and organization-wide strategy.
An independent international study investigated more than 100 production companies who had implemented Theory of Constraints (TOC) in their organizations. Previous published research on the application of TOC in the production industries has resulted in the following mean outcomes:
- 116% profit, throughput
- 83% increase in revenue
- 60% improvement in on-time delivery
- 50% inventory reduction
- 69% lead time reduction to produce products
- 66% cycle time reduction
Course Objectives ›
- Identify your real opportunities for production improvement- Find the key leverage points to focus your available resources on exactly the right area
- Improve production operation flow and logistics
- View your organization as part of the supply chain and begin to address your problems accordingly. Your exposure to the incredibly simple and powerful Drum, Buffer, Rope solution gives you the operational control valve for flow
- Reduce the amount of work in progress in production, giving every employee a much better chance of meeting customer due dates
- Discover why efficiency is the enemy of flow
- Deliver more production projects on time, on budget and within scope
- Define a new set of measurements for successful production projects - Find out why completing a task on time is no longer the best measurement and what to replace it with
- Get better results no matter how or when Murphy strike
- Identify and overcome assumptions from the past- Understand a powerful, proven production process used by top corporations
- Reduce cycle time on production projects significantly by remove the hidden padding from production projects and discover how to increase the capacity of existing resources by 25% or more
- Enhance in-place improvement efforts such as Lean, Just-in-time and Total Quality Management - Many good methods fail to get significant results because they are applied everywhere at once. Theory of Constraints (TOC) helps you apply them selectively in the most critical areas, so that you will be able to work effectively
Course Outline ›
Introduction & Agenda
- What "productivity improvement" really means
- Difference between physical and invisible constraints
- The 5 Focusing Steps to managing constraints
- Identify the Constraints
- Decide how to exploit the constraints
- Subordinate & synchronize everything else to the above decisions
- Elevate the performance of the constraints
- If in any of the above steps the constraint has shifted, go back to Step
- Case Study: Applying the 5 Focusing Steps
- The conflicts behind current decision-making in Production Operations
- The Problems with Cost Accounting and Activity Based Costing
- Bringing Deming (Statistical Process Control) and Goldratt (Theory of Constraints) together for major production improvement
Symptoms of Problems in Production Operations
- Defining a symptom- the "Undesirable Effect"
- Real-Life Example- Some orders are delivered incomplete
- Participant's Undesirable effects in Production Operations
- Connection between symptoms and root problems (The Disease)
Production Operations: Root Problem Diagnosis
- The System Approach- Introduce a systematic set of processes to manage production operations
- Overview of the 5 Thinking Processes
- Case Study: Production Operations flow problem in an actual company
Through simulation exercise, you will experience powerful new insights into how to significantly improve flow in any production operations environment. You will learn how to diagram a conflict behind a problem and understand how deeper problems can be analyzed this way - The core problem of Production Operations- Efficiency Measurements
- Open Discussion: Why 100% utilization of most resources is a bad idea
- The Solution
- Measurement in the Throughput world
Production Operations Simulations
- Introduction to computer simulations
- First Simulation: The Problem in all production operations environments
- The Deming approach to common cause variation
- Applying the 5 Focusing Steps in the simulation
- Second Simulation: A system's approach
- Drum, Buffer & Rope Solution
The Drum-Buffer-Rope method used to schedule operations, allows one to set the pace of the process (Drum), provide an allowance for 'Murphy' (Buffer) and control material release (Rope) - Implementation Solution
Open Forum On Day 1 Topics
- Open forum & review of participants' expectations and key questions
Conflicts Behind Undesirable Effects
- Why compromises fail to solve production operations' problem
- The Conflict Resolution Diagram
- Class Exercise: Building conflict diagrams from undesirable effects
Conflict Resolution
Learn how to use the conflict resolution DIAGRAM and negative branch techniques to deal with conflicts in production operations with one other person, empowerment issues, internal decision making difficulties. You will also be introduced to systems conflicts and the TOC approach. - Uncovering hidden assumptions that prevent solutions
- Injections: The breakthrough in eliminating production operations problems permanently
- Defining a Core Conflict- School & Class Example
Critical Chain for Production Project Management
- The challenge for reducing cycle times in production projects- 25% or better
- The Multi Project environment- Too many projects, not enough time
Participants would be able to see the effect of pushing too many production projects (Excessive order) into a system. You will learn the difference between good and bad multitasking. In this session, you will discover how to significantly reduce bad multitasking through staggering production projects correctly (The use of Drum and Strategic Resource buffers) - Multi tasking simulations- Doubling the number of production projects completed
- The constraints of the single project environment- Protecting the wrong thing
- The Solution Part I: Protecting the Production Projects- not the tasks
- The Solution Part II: Managing by Buffers
Supply Chain
- "The Goal" video
- Identifying the constraints in a supply chain
- Dealing with the constraints in a supply chain
- Example
The Next Step
- Discussion of participant situations and case studies
- Current cases & issues in production
Open Forum On Day 2 Topics
- Open forum & review of participants' expectations and key questions
Contact Us Now ›
|
|
![]()
|
![]() |